Material Driven Scheduling
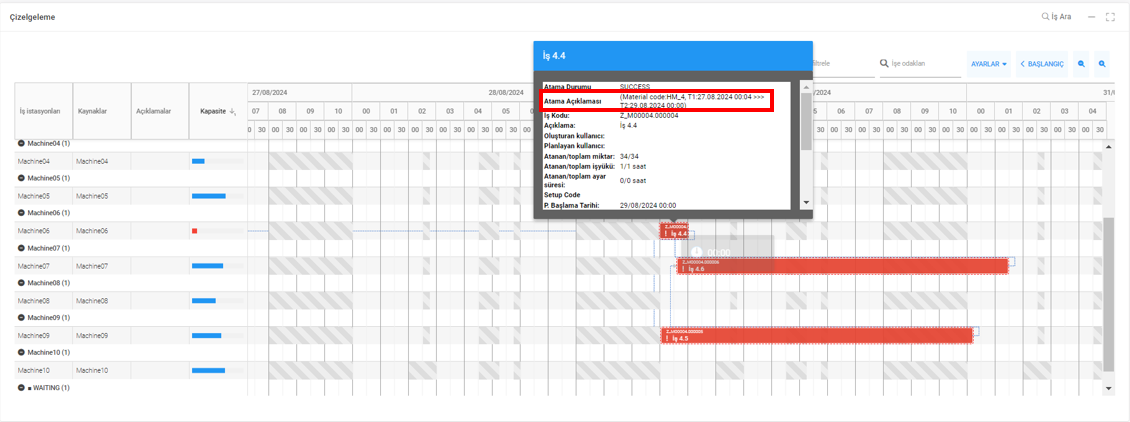
- Available Stocks: Consumption of existing stocks is planned according to the priority order defined for work orders.
- Purchase Orders: According to the delivery date of purchase orders, material consumption can be planned, work delays caused by purchasing can be reported.
- Bulk Semi-Finished Work Orders: Work orders are multi-level and may not be able to be integrated from ERP. When scheduling a multi-level job, the jobs are scheduled by creating a predecessor-successor relationship between the levels automatically by the software. In this case, planning can be done by dividing and associating sub-work orders as needed for the upper-level work order or as much as the batch size. No matter how many product tree levels there are, the association can be calculated quickly.
- Multi-Facility APS Integration: The production plan of more than one facility can be planned separately. The product produced by one facility can be defined as a raw material input in another facility and a connection between facilities can be established.
- Phantom Stock Solution: The inclusion in the plan of materials that are not in stock (Phantom) and for which a production work order has not been opened can be controlled parametrically. If there is no material required for the production of the finished product/semi-finished product in the work order, the program can offer solutions in two different ways. Due to lack of material, the work order can be not scheduled and reported, or scheduling can be done and the date on which the relevant material is required can be reported. This may also be called schedule-based MRP, and a purchasing or production work order proposal report can be presented.